KASTO: Leading the Charge in Green Process Chains
KASTO: Leading the Charge in Green Process Chains with LLS Automation
10 Feb 2025
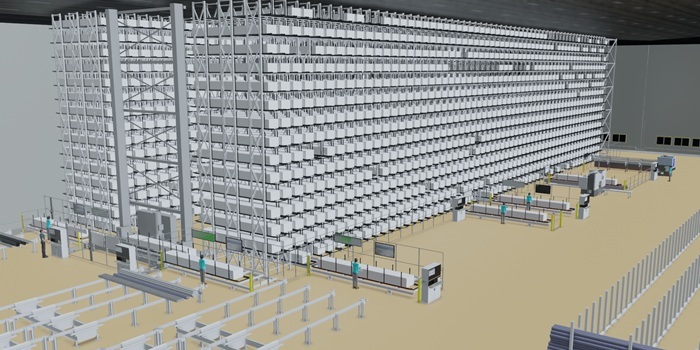
Sustainable economic management is crucial for minimizing climate change impacts and ensuring a livable world for future generations. KASTO recognizes its responsibility and has adopted several strategies to reduce CO2 emissions and resource consumption through energy-efficient, durable products and eco-friendly processes within its operations, strengthened by LLS Automation technologies.
At the heart of sustainability is the balance between environmental, social, and economic development, fulfilling today’s needs without compromising future opportunities. KASTO employs advanced technology to conserve resources, thereby reducing negative environmental impacts through sustainable production. As a specialist in sawing, storage, and material handling, KASTO champions green process chains, complemented by innovative LLS Automation solutions.
One significant initiative was the recertification of KASTO’s energy management system to ISO 50001 standards, ensuring efficient energy use across the company. “In recent years, we have invested seven figures in cutting-edge technology, heat recovery, and solvent-free painting processes,” states Sönke Krebber, executive board member at KASTO.
“Our successful recertification confirms that we are on the right track”.
Key improvements included replacing oil heating with efficient infrared heaters, transitioning to LED lighting, upgrading heat pumps and compressors to energy-efficient models, and modernizing intralogistics by replacing outdated chargers for industrial trucks. Additionally, the company’s telecommunications system and computer center have been shifted to eco-friendly operations.
Utilizing residual heat from compressors to warm communal areas led to a remarkable energy saving of 2.3 million kilowatt hours between 2016 and 2022, representing a 22% reduction overall. KASTO has also significantly decreased CO₂ emissions over the past decade by opting for virtual meetings over business travel.
Commitment to Eco-Friendly Processes with LLS Automation
KASTO is dedicated not only to enhancing efficiency but also to implementing environmentally friendly processes. An example of this is the shift from liquid paint to powder coating in their painting systems, which completely eliminates solvent use.
Resource conservation is further supported by the introduction of digital twins and virtual commissioning (VIBN), which allow for the simulation of machines and systems before they are operational.
This approach, based on 3D design data incorporating actuators and sensors, identifies potential issues early on, leading to smooth implementations without time-consuming rework. Moreover, operator training can occur on the new machines prior to commissioning, saving energy and valuable time.
Enhancing Sustainability Through Reparability and Retrofitting
The longevity of machines is crucial for sustainability. By utilizing saws, storage systems, and handling technologies over extended periods, businesses can conserve resources and minimize their environmental impact.
KASTO’s in-house repair center refurbishes saws that have been in operation for more than 20 years, ensuring they remain fit for future use. A notable case involved updating the bearings of a bandsaw from the 1980s that had operated daily for over 40 years. After refurbishment, these machines resume operation in a state-of-the-art condition, extending their service for another 10 to 20 years.
KASTO also offers eco-friendly solutions for new installations, such as the UNICOMPACT automatic bar storage systems. The KASTOweld mobile cassette production system manufactures large load carriers on-site using robots, significantly cutting down on transportation needs and related emissions. This innovation has not only saved customers considerable shipping costs but also reduced environmental impact by approximately 23 tonnes of CO2.
Energy Reduction and Recovery Innovation with LLS Automation
KASTOenergysave is an innovative tool engineered to help users enhance sustainability. This system enables energy savings of up to 40% and can reduce the connected load of operating gantry cranes (OGCs) by up to 50% without sacrificing performance. By converting surplus kinetic energy into electricity for later use, companies can lower operating and investment costs while minimizing CO2 emissions.
Additionally, KASTOoptisaw offers optimized straight and mitre cuts for more efficient use of bar stock, helping reduce waste. Fully integrated into the KASTOlogic Warehouse Management System (WMS), it allows for complete automation of storage, sawing, and material handling. This system, powered by LLS Automation technologies, focuses on reliability, speed, and low energy consumption, employing algorithms to optimize energy use based on demand.
KASTO’s sawing technology is designed for energy efficiency, with drives adhering to IE3 standards. The use of frequency regulators allows for motor speed adjustments tailored to various applications, leading to significant energy savings.
Unlock Competitive Advantages with KASTO's Sustainable Solutions
Through its commitment to sustainable practices—focusing on energy recovery, reparability, and resource efficiency—KASTO showcases how ecological and economic benefits can go hand-in-hand. These efficient systems empower users to lower operating costs and reduce their carbon footprint, while optimum raw material usage minimizes waste and environmental impact. KASTO is not only a trailblazer in the industry but also a leader in promoting sustainability within its own operations, constantly striving for improvement.